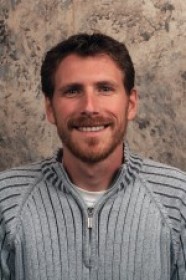
11:00 am to 12:00 am
Event Location: NSH 3002
Abstract: Assembly is a task at which robots excel, but only as long as they operate in well-controlled environments such as factories or assembly lines. This thesis presents a comprehensive planning and execution framework that enables mobile manipulator robots to overcome this limitation and assemble large structures in physically challenging environments. In order to be useful in realistic scenarios, the developed system must be robust to inevitably occurring execution-time failures, generate plans efficiently and scale to large problems including complex structures being assembled by multiple robots.
Complex tasks today are approached in one of two fundamental ways: as a problem of sequencing abstract tasks, or as fine-grained motion planning problems. The prior has no problem reasoning about large problems, but lacks understanding of the physical context of the scenario, whereas the latter considers physical reality but lacks the scope for complex scenarios. This thesis develops a graph-based representation that exploits synergies between both methodologies to solve large, physically grounded problems.
Beyond planning complex assembly tasks, the fundamental challenge for a useful system lies in its ability to successfully execute the planned task even when unforeseen problems occur during operation. Comprehensive repair and re-planning strategies are essential to avoid terminal failures, and ultimate robustness is achieved by allowing an expert operator to assist with error recovery at the behavioral, executive and planning levels as appropriate.
Once assembly plans can be executed reliably, the efficiency of plan generation can be improved both when finding the initial plan, as well as when repair and re-planning become necessary. The techniques presented in this thesis reduce the planning time required by 2.5 orders of magnitude and more compared to a baseline solution. These improvements make the system practical to be applied to larger problems. Hierarchical problem decomposition, as well as computational and physical parallelization, allow the framework to scale to large structures of hundreds or thousands of components being assembled by multiple robots.
The comprehensive assembly planning and execution framework developed in this thesis pushes the boundary of what mobile manipulator robots can accomplish in realistic environments. It provides the high-level intelligence necessary to apply low-level capabilities to very large problems, and it includes error recovery strategies to cope with inevitable exceptions while performing complex and challenging tasks.
Committee:Sanjiv Singh, Chair
Reid Simmons
James Kuffner
Randy Wilson, Google, Inc.