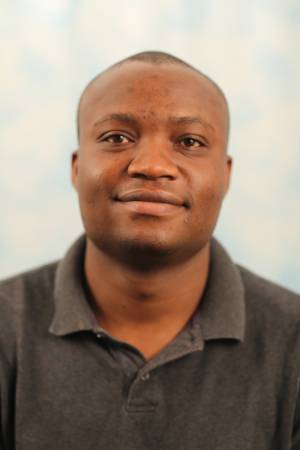
Abstract:
Although agriculture is a highly mechanized industry, numerous sectors like horticulture and floriculture heavily depend on manual labor because they require safe handling of plants and produce that can only be left to humans. However, many research and commercial robots have succeeded in several challenging dexterous manipulation tasks like harvesting, pruning, and plant health monitoring. These robots are typically designed as monolithic systems that are expensive to develop and, as a consequence, are prohibitively costly to adopt for regular farm use.
Using modular, reconfigurable robots (MRRs) for mobile robot manipulation in agriculture enables the automation of complex tasks with versatile and robust systems that offer cost-effective designs tailored to specific requirements. Researchers also benefit from MRRs, as they reduce non-recurring engineering costs, freeing up resources for critical areas of investigation. However, using MRRs presents a significant challenge: given an MRR system, how can a user generate the optimal design for their task? This problem is difficult, even for experts, and becomes more complex for mobile manipulation robots operating in highly cluttered environments.
In this thesis, we introduce an automated robot reconfiguration pipeline designed to solve the challenge of obtaining the best robot design for the task when using modular reconfigurable robots. We adopted a robot optimization framework that breaks down the design problem into (a) the robot model, (b) task and environment representations, (c) the task performance metric, and (d) the optimizer. This approach allows the users to choose their preferred MRR system, task description, and environment.
We introduce new task metrics evaluation methods for manipulation and navigation to deal with highly cluttered environments. For manipulation, we develop a new inverse kinematics solver for redundant manipulators that can efficiently obtain a solution if it exists. We also introduce a new approach to measuring the robot’s capacity to navigate a crop field without colliding with obstacles. With the addition of better environment representations, we seek to obtain the best MRR configurations for mobile manipulation in real-world agricultural tasks.
The results of this work will enhance the adoption of mobile manipulation robots for challenging agricultural tasks that require specialized skills and often go understaffed. Many stand to benefit from the automated robot reconfiguration tools proposed in this work: farmers and agronomists will improve labor efficiency, experts will save time, and researchers will reduce R\&D costs.
Thesis Committee Members:
George Kantor, Chair
Oliver Kroemer
Zeynep Temel
Changying (Charlie) Li, University of Florida