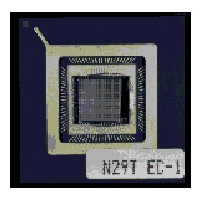
We have built a high-performance VLSI sensor which consists of an array of photosensitive cells which independently determine when they see light from the stripe reflected back by objects in the scene. Working in parallel, the array of cells acquires a 1,024 pixel range image in a millisecond. The accuracy and repeatability of each pixel has been measured to be within 1.0 mm at 500 mm distances (0.2%). The range-image frame rate is limited solely by sensor photo-detector bandwidth and is, in sharp contrast to conventional light-stripe techniques, independent of range image spatial resolution.
The integration of sensing and processing using VLSI technology is the key to the sensor’s performance. The 3-D measurements are made in parallel at each pixel site by continuously analyzing the observed intensity. A small amount of local computation in each cell results in a tremendous reduction in data bandwidth.
A second-generation range-sensor chip is now operational. The cells of this new design are 40% smaller and employ a "true-peak" detector to measure stripe timing, replacing the thresholding circuitry used in the first-generation design. True-peak detection is a more robust means of stripe detection. The second-generation sensor operates on a wide variety of objects, unaffected by indoor ambient lighting. In addition, scene reflectance data is acquired with range data as an artifact of the peak-detection process. The pixels of the reflectance image are perfectly aligned with corresponding range-image pixels. The reflectance images assist in device calibration and provide additional sensing capability to applications.
Now that the basic range-imaging technology has been successfully demonstrated, we are exploring use of the VLSI range sensor in robotic applications. Potential applications include whole shape measurement of a vehicle or aircraft, the design and inspection of manufactured parts, robotic manipulator control, 3-D imaging of the human body for use in reconstructive surgery, control of surgical instruments during an operation, design of protective equipment and tailoring in the fashion industry.
In the first application that used the prototype sensor, we demonstrated full 3-D pose estimation of arbitrarily shaped rigid objects at speeds up to 10 Hz. We will continue to work on moving this technology from the laboratory and ultimately deploy compact range systems for use in university, industrial and medical robotics research.