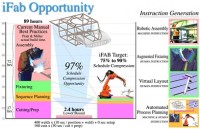
Many manufacturing processes require considerable setup time and offer a large potential for schedule compression. For example, Pratt&Miller Inc. constructed a military spec HMMWV welded spaceframe with best-practice methods, this took 89 billable hours — cutting square tubes, preparing them for welding, and then performing the final welding tasks to build the structure. On analysis, we discovered that the time actually spent on constructive processes was only 3% (slightly over two hours) of that total. Thus 97% of the overall time can potentially be eliminated. We built a system to exploit this opportunity that includes a welding robot, an augmented reality projection system and a laser displacement sensor. To test the system, we fabricated a custom variant of a HMMWV welded spaced frame where pre-process tasks were automated: BOM acquisition, component preparation, sequence planning, weld parameter optimization, fixture planning, workpiece localization and finally automated work assignments were delegated to a robot and a person. In the end, we were able to make the custom welded product nearly 9x faster than was previously possible. This achievement also translates economically to the bottom line because the cost of raw materials was only 6% of the total costs. This talk will highlight the technical achievements that made this possible.
current head
current staff
current contact
past staff
- Michael Dawson-Haggerty
- Gregg Podnar