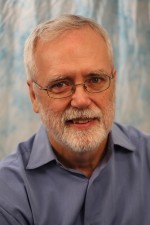
I am formally retired at CMU, although still supervising students as they finish and graduate. Most of my activity has shifted to my position as Chief Scientist at Berkshire Grey. (RI Seminar about warehouse automation at Berkshire Grey.)
I work in robotics.
The primary venue for my work was the Manipulation Lab (MLab).
Simple Hands
My primary focus is simple hands. I think simple hands are better than complex anthropomorphic hands, both for research purposes and for most applications. The main reason is that the dexterity of a hand is mostly about the brain, not the hand. Our approach mixes a strong dose of machine learning into the traditional brew of AI, control and mechanical design. If you’re curious, there are publications here. Probably the first one to read is the 2012 IJRR paper Autonomous Manipulation with a General-Purpose Simple Hand. Also see related papers from ICRA 2013 and RSS 2011, both of which won best student paper awards. The project is mostly funded by the National Science Foundation.
Direct Drive Hand (DDHand)
Much of our simple hands research shifted to the use of direct drive technology. The advantages of direct drive are well-known, but had not previously been applied to hand design. The DDHand project is a collaboration with Ankit Bhatia who envisioned it and leads the project, and Aaron Johnson. Look for the 2019 RSS paper with Bhatia and Johnson, and a paper to be published, we hope, in IROS 2022.
Extrinsic Dexterity
In robotic manipulation lingo, “dexterity” often refers to moving an object in the hand, like when you drop a coin from a fingertip grasp to your palm. However, most research on dexterity assumes a complex anthropomorphic hand. Under the standard assumption, a simple hand cannot shift grasps. But those assumptions are too restrictive. We have demonstrated the mechanical feasibility of dexterous manipulation using a simple hand. Our research is focused on going beyond mechanical feasibility, so that an autonomous robot could employ extrinsic dexterity by planning and controlling the simple hand for a given object and task. The first paper to read is the 2014 ICRA paper (Chavan Dafle et al.), perhaps followed by the Zhou et al. paper which won Best Conference Paper at ICRA 2016, a subsequent WAFR 2016 paper by Hou et al., or most recently a forthcoming paper recently submitted to ICRA 2022.
Compliant Control
Advanced manipulation depends on compliant control. While the DDHand has great advantages in compliant control, Yifan Hou led efforts to re-define and improve hybrid force velocity control, and applied the control to a variety of dexterous manipulation tasks. See papers by Hou et al., in ICRA 2018, IROS 2019, WAFR 2020, and RSS 2020.
Contact modes, automatic planning of manipulation primitives
Rigid body contact is often modeled in terms of contact modes: each contact between bodies can be separating, fixed/rolling, or slipping. Simulations and automatic planning may depend on identifying the contact mode, but, amazingly, algorithms for enumeration of contact modes in 3D were not available until the project led by Eric Huang. See the forthcoming paper in IJRR by Huang et al. Contact modes also play a prominent part in recent dexterous manipulation planning led by Xianyi Cheng. Combining our work on robust compliant control, enumeration of contact modes, Xianyi is exploring the use of sampling-based planning, biased towards maintaining contact modes, to obtain efficient planning of practical dexterous manipulation. See Xianyi’s 2021 ICRA paper, or a forthcoming 2022 ICRA paper.
Manufacturing Automation
Industrial automation is the ultimate proving ground for robotic manipulation research, and an important source of technology and ideas. A recent project sponsored by Foxconn focused on automatic assembly of smart phones. The challenges are formidable, since smart phones use very small parts, some floppy and some sticky, and there is unavoidable clutter. Look for our paper surveying threaded fastening automation, and a paper on machine learning applied to classify stages of screw insertion (ISER 2016). More recently we worked on the assembly of an automotive door latch, described in a paper we hope will be published in IROS 2022.